在制造业高速发展的今天,挤出机作为塑料、橡胶、食品加工等领域的核心设备,其操作规范直接影响产品质量与生产效率。据统计,超过60%的设备故障源于操作不当或流程疏漏。本文将系统拆解挤出机操作流程和步骤,帮助操作人员掌握从开机准备到停机维护的全流程要点,确保生产安全与效能双提升。
一、操作前的核心准备工作
“工欲善其事,必先利其器”,挤出机的稳定运行始于周密的准备工作。
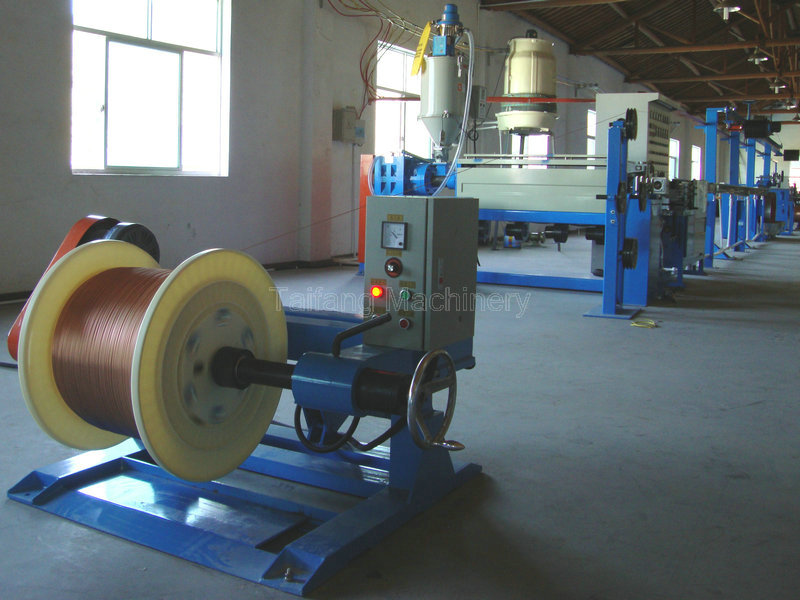
- 设备检查清单
- 电气系统:确认电源电压稳定(通常为380V±5%),检查控制柜线路无老化、松动;
- 传动部件:润滑齿轮箱油位(推荐使用ISO VG 220齿轮油),测试螺杆转动是否卡顿;
- 温控模块:预热加热圈至工艺要求温度(例如PVC加工需设定180-220℃分段控温),误差需控制在±3℃以内。
- 原料预处理
- 根据材料特性进行干燥(如尼龙需在80℃下干燥4小时),避免水分导致气泡;
- 筛网目数选择:金属杂质过滤推荐80-120目,确保熔体纯净度。
二、开机操作的关键步骤分解
操作阶段是产品质量的核心控制点,需严格遵循标准化流程。
- 启动顺序标准化
- 先开启冷却系统(冷却水流量控制在5-8L/min),后启动主电机(低速运行5分钟磨合);
- 采用阶梯式升温:每10分钟提升20℃,避免温度骤变引发热应力。
- 喂料与参数调试
- 双阶喂料法:初期以30%负载运行,待电流稳定后逐步提升至额定值;
- 扭矩监控:主电机电流波动需<5%,异常时立即停机排查堵料或螺杆磨损。
三、运行中的动态监控策略
“三分靠操作,七分靠巡检”,实时监测是规避风险的核心手段。
- 多维度数据采集
| 监测项 | 标准范围 | 异常处理措施 |
|————–|——————-|—————————|
| 熔体压力 | 8-15MPa | 超压时检查滤网堵塞情况 |
| 螺杆转速 | 20-60rpm | 振动异常需校准传动轴同心度|
| 出料均匀度 | 厚度误差≤0.1mm | 调整模唇间隙或温度梯度 |
- 应急响应机制
- 突发停电时立即关闭加热电源,手动盘动螺杆防止物料碳化;
- 紧急制动按钮测试:每月至少进行1次功能性验证。
四、停机维护的黄金法则
规范的停机操作可延长设备寿命30%以上,避免隐性损耗。
- 渐进式停机流程
- 停止喂料后持续运转至机筒排空(通过观察口确认无残留);
- 降温策略:先关闭加热器,待温度降至80℃以下再停冷却系统。
- 深度保养计划
- 螺杆清洗:使用专用清洗料(如PP基料)进行3次以上置换;
- 关键部件检查:测量螺杆与机筒间隙(磨损量>0.5mm需修复镀层);
- 润滑系统更新:挤出机减速箱每年更换一次全合成润滑油。
五、安全操作的红线警示
“安全是1,其他是0”,以下操作禁忌必须牢记:
- 严禁戴手套操作旋转部件,袖口、长发需严格固定;
- 机筒未冷却至60℃前禁止拆卸模具(防烫伤及材料回弹);
- 绝对禁止超负荷运行:电流持续超过额定值10%必须停机检修。
通过以上系统化的操作流程管理,企业可将挤出机故障率降低40%以上,同时提升产能利用率15%-20%。数据显示,规范操作可使吨能耗下降8%-12%,这对实现绿色制造与成本控制具有双重价值。