在金属线材加工领域,管绞机的”穿线”环节直接决定着生产效率和成品质量。 这项看似简单的操作,实则涉及机械结构认知、张力控制、路径规划等关键技术。本文将以工业级管绞机为对象,系统讲解穿线操作的规范流程与进阶技巧。
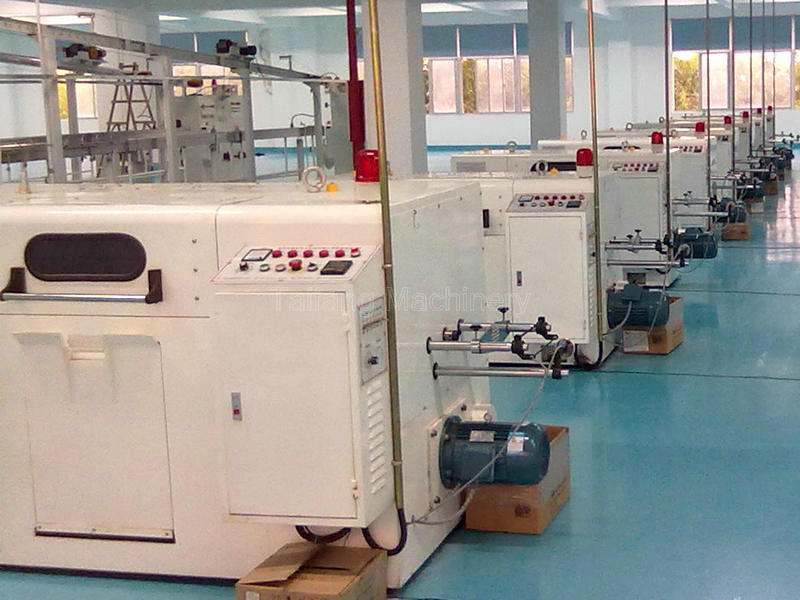
一、穿线前的核心准备
操作管绞机前,需确保设备处于 断电锁定状态 并完成三项关键检查:
- 绞盘清洁度:用高压气枪清除残留金属屑,特别是线槽内的氧化层(建议使用0.6MPa压缩空气)
- 导向轮校准:用激光定位仪检测各导向轮平面度,偏差需控制在±0.1mm以内
- 张力系统验证:空载状态下测试电磁制动器响应速度,标准值为0.2秒内完成制动力建立
某线缆企业实践数据显示,规范执行预处理可降低83%的断线概率。
二、7步标准化穿线流程
步骤1:线材预处理
- 剪切线头形成15°斜角(建议使用液压剪线钳)
- 涂抹专用润滑剂(铜线推荐使用Teflon基润滑剂)
步骤2:进线路径规划
- 遵循”3点成弧”原则:进线轮→张力轮→绞盘入口应形成平滑曲线
- 错误案例警示:某工厂因路径直角弯折导致月均断线47次
步骤3:穿线机械操作
- 打开防护罩锁定装置(需同时按下双联安全开关)
- 将线头穿过导轮组(注意保持与旋转方向同向)
- 手动旋转绞盘2圈预缠绕(扭矩控制在5-8N·m)
步骤4:张力系统设置
- 初始张力=线材抗拉强度×0.15(例:2mm²铜线设为12-15N)
- 动态补偿系数建议值:铜材0.8,铝材1.2
步骤5:自动化测试
- 以10%额定速度试运行(时长不少于30秒)
- 观察线材轨迹波动幅度(标准值<±1.5mm)
步骤6:生产参数优化
- 绞距计算公式:D×(π/tanα)(D为绞合外径,α为提升角)
- 典型参数组合:Φ200绞盘配0.5mm线径时,转速宜设为350rpm
步骤7:质量验证
- 抽样检测绞合节距误差(行业标准为±2%)
- 使用微欧计测量导体电阻(波动率应<3%)
三、5大常见故障解决方案
故障现象 |
可能原因 |
解决方案 |
线材跳槽 |
导向轮磨损>0.3mm |
更换陶瓷导轮并调整间距 |
绞合不紧 |
张力不足或转速过高 |
按公式T=K×d²调整(K值取0.15-0.3) |
表面划伤 |
过线导板粗糙度超标 |
使用800目砂纸抛光处理 |
断线频发 |
穿线路径存在锐角 |
增加过渡导轮改善曲率 |
绞距不均 |
主轴编码器信号异常 |
清洁光电传感器并校准 |
四、进阶维护策略
实施预防性维护可提升设备综合效率(OEE)12-18%:
- 每周检查:轴承温度(标准<65℃)、齿轮箱油位
- 每月维护:清洁电磁离合器工作面(使用99%纯度酒精)
- 季度保养:更换减速机润滑油(推荐ISO VG220级)
- 技术要点:采用振动分析仪监测异常频率(重点关注800-1200Hz波段)
通过掌握这些关键技术要点,操作人员不仅能提升穿线效率,更能显著降低设备故障率。数据显示,规范操作的工厂其线材成品合格率可从89%提升至97%以上。